Robotic Assembly Line. Allied Leads Industry in Innovation with First-in-the-World Robotics Line at our New Manufacturing Facility In McGregor, TX
Known for innovative thinking, Allied’s limitless mindset applies not just to clients’ projects but to our own endeavors, as we explore new ways to evolve and improve our capabilities. After making bold moves by opening our first manufacturing facility in La Coruna, Spain in 2020, we recognized a growing demand for Allied’s high-quality manufactured steel and have taken another major leap forward with the construction of our second facility in McGregor, Texas. In addition to bolstering our production capacity, this expansion will feature a one-of-a-kind robotics line, on-site solar power reducing our carbon footprint, and state-of-the-art manufacturing equipment, making it the leading technology facility in our industry.
Robotic Assembly Line – A Technological Transformation
Anticipated to revolutionize the way Allied produces steel assemblies, the custom robotics line from Lincoln Electric/Zeman is the first of its kind in the world. By fully automating all assembly and welding processes, this ecosystem of four cutting-edge machines and integrated software will redefine what is possible in terms of quality, precision, and the speed of these phases in steel buildings manufacturing. This groundbreaking new system has the potential to transform more than just key industry processes and, once operational, will provide unprecedented employment opportunities in the fields of steel assembly and robotics. Allied is eager to invest in the local workforce and work together towards shared goals of advancing the state of steel building manufacturing.
Steel parts will begin their journey through this groundbreaking new system in a Scanning and Plate Sorting (SPS) machine, where they will be scanned, identified, sorted, and allocated based on project needs. From here the automated system will transport the parts to the steel beam assembler (SBA) machine, where robotics will position, hold, and secure the parts to form assemblies up to 40′ long. The final two machines are identical Steel Beam Welders (SBW) that will work in tandem to weld the assemblies into their final desired form.
An automated guided vehicle (AGV) and conveyor system will transport the parts between the various machines in a continuous and highly precise workflow unlike any other in the world.
All components of the robotics line communicate not only with one another, but with sophisticated software that interprets and communicates each project’s needs and even has the capacity to assess whether or not design configurations are optimized for the line. Despite the extraordinary degree of automation, the system is designed with flexibility in mind, allowing beams to be welded manually whenever needed, without interrupting the workflow.
In addition to improving the speed and quality of production, the system will leverage modeling technology to identify and solve potential design flaws before they occur. With this unprecedented robotics line, Allied aspires to set new industry standards, passing on significant cost and time savings to our clients.
Building a Collaborative Future
The success of this operation depends on the people who run it and as the technology behind welding evolves, Allied recognizes more than ever the need for skilled and experienced professionals who know the trade. With esteemed institutions including Baylor University and TSTC nearby, we are enthusiastic about sharing our expertise and products while providing opportunities for skilled local individuals to contribute to cutting-edge advancements in automation and manufacturing. Our expansion in McGregor signifies a bright and promising future for both Allied and the McGregor community, with an immense potential for growth.
Redefining What is Possible
With this milestone accomplishment, we continue to demonstrate that we are a company of action, always pushing for new solutions that improve our capabilities. It’s just one of the many reasons we’re trusted by clients worldwide to tackle the most intricate challenges, and build legacies for generations to come.
Follow our progress:

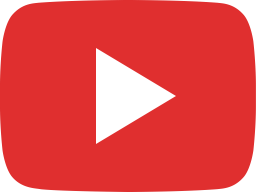
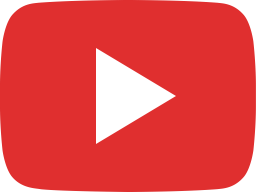
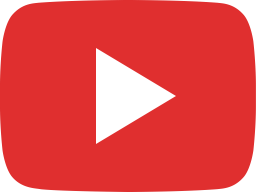
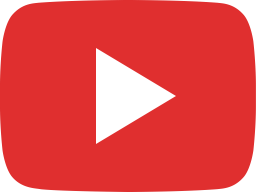
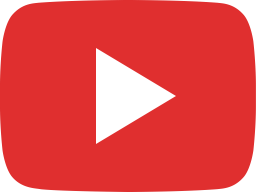
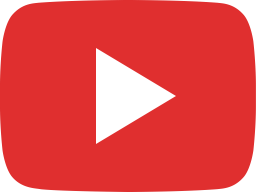
