A product fulfillment business is only as successful as its day-to-day warehouse operations. Whether you are planning your company’s first or hundredth distribution center design, the chosen layout can make or break productivity. Evaluate these essential distribution center layout considerations before finalizing your design.
Process Design
1. The Flow
First and foremost, assess the flow of products through your warehouse—from the initial receiving stage to the final shipping stage. With an optimized flow, you can process goods through your facility efficiently to avoid any backtracking or pinch points. Consider the flow of not only items, but also of personnel and equipment.
2. Optimizing for Storage
Logical product storage ensures efficient storing and picking operations. It’s important to incorporate enough storage in your distribution center layout to meet your current demands. Then, optimize the storage method—you can group products by type, popularity, or another factor specific to your business.
3. Equipment Spacing
Evaluate how equipment will move in and around your warehouse. Most equipment requires a certain amount of clearance from walls or other fixed objects, and you will also want to leave room for dedicated walkways for personnel out of equipment paths.
Types of Warehouse Equipment
The equipment often used for distribution center operations includes: pallet jacks, forklifts, conveyors, and other lifting and packing tools. Most forklifts require a minimum aisle width of 12 feet to maneuver through a warehouse safely.
4. Plan for Growth
In a perfect world, your business will grow and expand over time — and your distribution center will need to expand with it. Consider any future expansion ideas while planning your initial distribution center design layout. Choose a layout that easily allows expansion of your storage area or the addition of more loading docks.
5. Employee Considerations
Last, but certainly not least, consider your employees’ needs while designing your distribution center’s layout. Think about the number of employees you currently have, their skills and abilities, and how your layout can assist in increasing productivity. Additionally, think about how future employees would work within the layout.
Physical Design: The Building and Its Components
6. The Building
Your distribution center’s physical shape will likely be one of the first discussion points when configuring your distribution center layout. There are three standard warehouse designs to choose from according to distribution center best practices: U-shaped, I-shaped, and L-shaped. Each layout option offers different locations for your shipping, receiving, and storage areas. Consider customizing one of these standard distribution center layouts to meet your company’s needs.
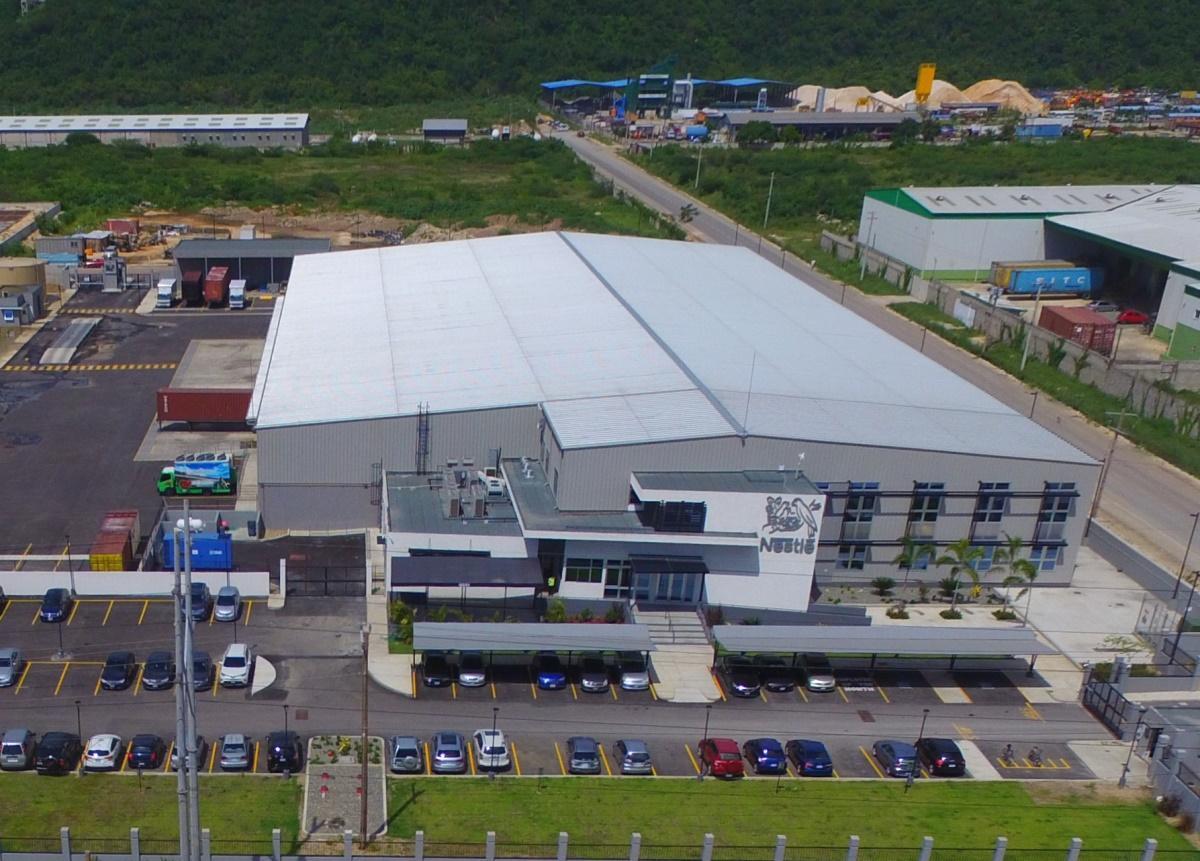
DCIM100MEDIADJI_0192.JPG
7. The Docks – Shipping and Receiving
Your shipping and receiving docks facilitate the flow of products through your distribution center. Due to the criticality of these docks, it is essential to perfect the design. Ideally, your shipping and receiving docks will be located at the opposite ends of your warehouse to limit truck traffic congestion.
8. Reception
Once a product is received off the loading dock, it should be set in a reception area immediately inside the facility. Within the reception area, leave enough space for the inspection and quality control processes and access to an aisle for a forklift or pallet jack to take the products to storage.
9. Storage
Distribution center storage areas typically use vertical storage, like shelving systems. The product shelves can extend from wall to wall and floor to ceiling to maximize storage. Product storage can be organized using various standardized methods, including separating static items from dynamic items.
Static Storage
Static storage is for items that typically do not fly off the shelves. These items may be seasonal or just have a lower order volume. Use higher shelf racks or back areas that are more difficult to access to store static items.
Dynamic Storage
Dynamic items have the highest order volumes, therefore, must be easily accessible. Place dynamic storage front and center in your storage area, allowing simplified access for forklifts or pallet jacks.
10. Picking
Warehouse picking, the process of locating a product to fulfill an order, can be made more efficient with an optimized distribution center layout. Choose from one of the effective picking methods below and tailor your warehouse layout to that method.
Batch Picking
With batch picking, employees are expected to grab an entire batch of orders at one time. This method is highly efficient when employees have an organized list of orders to pick from.
Zone Picking
If a zone picking method is used, employees are assigned to a specific area in the warehouse. Employees fulfill only the orders with SKUs located in their designated zones.
Discrete Picking
Discrete is the type of picking most often used because it is a simple, straightforward process. With discrete picking, a single employee picks an order, one item at a time.
Wave Picking
Wave picking is similar to discrete picking, such that a single employee picks a single order; however, orders are only picked during a specific time of the day to maximize efficiency.
11. Packaging and Shipping
Once a product is picked, it is packaged and shipped out. Your packaging and shipping areas should be located between the picking area and shipping dock to keep the order of operations sequential. Be sure to account for the storage of packaging and shipping supplies in this area.
12. Office Space and Restrooms
Employee accommodations are an essential part of a distribution center layout design. Incorporate enough offices and restrooms throughout your facility to accommodate the number of employees per shift. Consider future warehouse expansion plans when determining the number of offices, bathrooms, and other employee facilities needed.
General Building Considerations
13. Utilities and Access
Like any other facility, distribution centers need access to certain utilities. The extent of utilities is not as far-reaching as a production facility, but distribution centers still require a minimum of electricity, water, sewer, and gas hook-ups. Additionally, ensure the distribution center site itself is easily locatable for employees and delivery drivers.
14. HVAC System
The HVAC system in a distribution center must be efficient and effective. These large spaces require a tremendous amount of resources to heat and cool. Therefore, ensure the HVAC system is sized appropriately for the entire facility and consider incorporating energy efficiency upgrades.
Radiant Floor Heating
Radiant floor heating is a popular heating method for warehouse buildings like distribution centers. A system of hot-water pipes and electrical wires embedded in the concrete floor heats the facility from the ground up. This method is much more efficient than forced air heating.
15. Resilient Flooring
The flooring throughout a distribution center takes on a lot of wear and tear. Consider installing resilient flooring—a non-textile type that offers both user comfort and long-lasting durability. Incorporate wayfinding marks on your flooring to designate aisles for equipment.
16. Warehouse Management System (WMS)
To view and manage your entire distribution center’s inventory and supply chain, use warehouse management system (WMS) software. There are many types of WMS software on the market that will help keep your business organized and locate areas to improve efficiency.
17. Parking Lot
The area around your distribution center needs just as much attention as the warehouse itself. Ensure that your parking lot can handle both employee vehicles and delivery trucks. Consider the expected traffic flow and design access roads accordingly.
Permeable Pavers
Consider installing permeable pavers within your parking lot to improve stormwater drainage and reduce runoff. Permeable pavers absorb rainwater to reduce the demand on your stormwater management system.
Trust in Allied Steel Buildings for the Best Metal Distribution Center Buildings
Ready to build your company’s next distribution center warehouse? Work with a team of experts who understand all of these essential considerations, and then some. Contact Allied Steel Buildings today to get your distribution center project started today.