When it comes to the modern construction landscape, the two methods that dominate the industry are concrete tilt-up and pre-engineered steel building construction. While both construction techniques have their advantages, each works best in different situations. Over the course of this article, we’ll take a detailed look at how concrete tilt-up and steel construction compare with each other.
Defining Tilt-Up Construction
Tilt-up construction involves the walls of a structure being horizontally cast on the ground before they are lifted and fixed to a pre-constructed foundation slab or edge beam. To ensure that the structure is stable and weather-proof, the adjacent units are connected together.
The Development of Tilt-Up Construction
Materials which originate from industrial or engineering applications often become adopted for their architectural or artistic potential. A good example is weathering steel, which was originally developed to be used in railway coal wagons in the 1930s, but became a popular building construction material in the 1960s.
Such success stories aren’t a rare occurrence in the world of architecture and construction. After all, the exploration of aesthetic and functional properties of otherwise basic construction materials has always been one of the signature characteristics of the discipline. However, this tendency didn’t really take off until the 20th century, when the idea of functionalism emerged. The boundary between form and function was regularly crossed in the modern and post-modern eras.
Although tilt-up construction has long since established itself as a popular construction technique, what’s surprising is that it didn’t start out as a general building solution. First pioneered in the 1920s by a Californian architect, Irving Gill, tilt-up construction was reportedly inspired by the engineering efficiency of factory assembly lines.
Simply put, tilt-up construction was developed as an efficient technique of raising a complicated concrete façade without needing to go through a tiresome vertical forming procedure. As the global economy dropped to an all-time low during the Great War, tilt-up construction rose in popularity because of its speed, convenience, and affordability.
There are many excellent reasons why the tilt-up method dominates the construction of flexible diaphragm, rigid wall large-box structures. It’s highly convenient and time-saving to cast the wall panel of these structures by using the vast floor slabs and then simply using cranes to raise them into place on structures that have relatively plain wall envelopes and uncomplicated perimeters.
However, the evolution of tilt-up construction means that the method is now even used in complex, multi-storey, irregularly shaped projects. As speed is tilt-up’s greatest advantage, architects and contractors get more time to focus on craft and quality.
In modern construction, tilt-up is regularly considered in building projects of all shapes and sizes. In the United States, 15% of all industrial buildings are tilt-up, ranging in size from 5000 to over 1.5 million square feet.
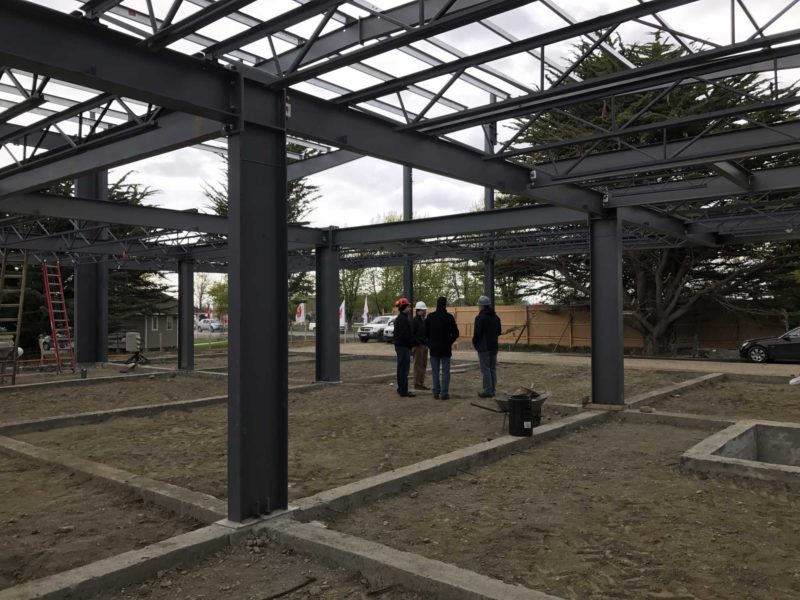
Preengineered steel building framing in Punta Arenas Chile
What Are Pre-Engineered Steel Structures?
Also known as pre-fabricated steel structures, these steel buildings are fully designed and manufactured in a factory before being shipped out to the build site to be erected using nuts and bolts, thereby reducing the completion time of the project.
The Evolution of Steel Buildings
The history of steel goes as far back as 4,000 years, when clever inventors and experimenters of the era found out that iron was a much better metal than bronze in terms of strength and durability. Since that moment, people have worked tirelessly to develop purer and purer forms of iron steel, which have been used as tools, weapons, railroads and lastly, as a construction material. In the modern day, steel is regarded as one of the most durable, eco-friendly and cost-effective construction materials there are.
However, it took millenniums for steel to develop into the incredibly tough and consistent construction material it’s known as today. Before the 17th century, steel was mainly used to manufacture weapons. By the 1800s, steel production had become more efficient and the material had evolved into a more durable and versatile building material.
The first building that featured a steel framework was built in 1793. Before steel became a commonly used construction material, industrial burning went up in flames on a regular basis. After a particularly devastating fire in 1803, the Belper North Mill in the UK was rebuilt with a frame entirely made out of steel. Incredibly, the building still stands to this day.
The late 19th and the early twentieth century saw the construction of some of the world’s first skyscrapers. Built in 1902, the Flatiron Building was among the first steel-framed skyscraper. The concept of pre-fabricated steel buildings emerged in the 1960s and today, nearly 70% of all commercial buildings in the United States are pre-engineered.
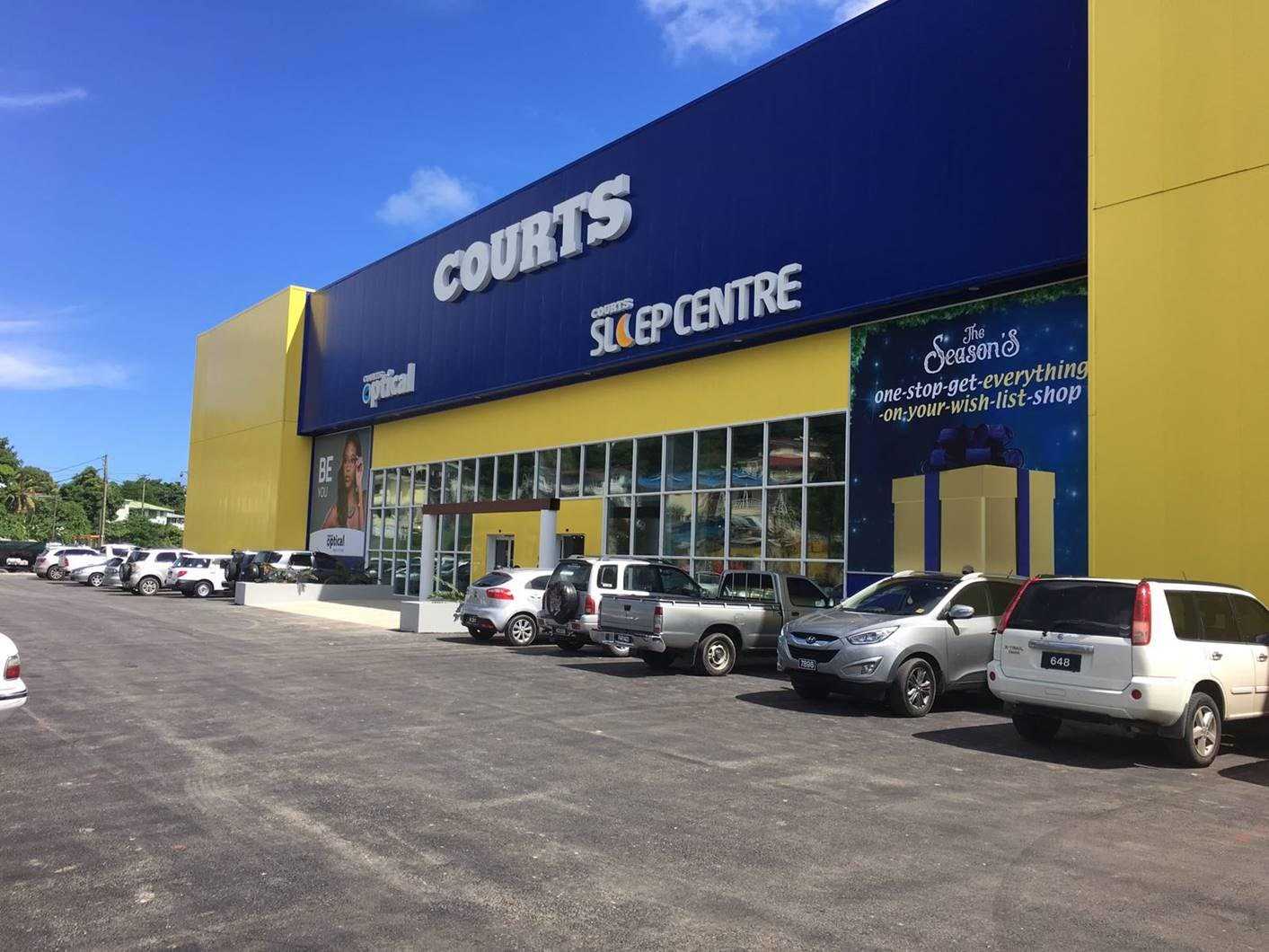
Blue & yellow, preengineered steel building in St Lucia Caribbean
Factors to Consider While Comparing Tilt-Up Construction with Steel Construction
As each commercial building project has unique parameters, there are a variety of factors to consider before you choose a construction method. These include:
- Building Size
- Availability and Usage of Materials
- Time
- Costs
- Design Possibilities
- Recyclability
- Durability
- Purpose of the Project
The Size of the Project is a Huge Factor
Perhaps the biggest factor to consider is the size of the build project. If the size of the structure is less than 50,000 square feet, steel construction is generally the more cost-effective option. Although concrete is a much less-expensive material than steel, tilt-up construction typically involves extra fixed costs, such as large crane rentals, which make it more expensive than steel in projects of this size.
However, with projects exceeding 50,000 square feet, the significantly lower material costs begin to counteract the higher fixed costs of tilt-up construction, thereby making it cost-competitive with steel construction. Tilt-up construction might actually be more cost-effective for large projects where the walls aren’t a significant percentage of the structural costs. Scale is a big issue when you compare these two methods.
As metal has a superior spanning capacity than concrete, pre-fabricated steel buildings are the better option for structures that require longer bays and spans. This especially applies to office buildings, as metal buildings offer more flexibility in terms of floor space. The advantage with metal buildings is that the depths and locations of columns can be customized, which makes it adaptable to the majority of floor plans. This becomes of consequence if you want to remodel in the future. Concrete construction requires a greater number of support columns. This creates limitations in terms of usable square footage and the moving of partitions and walls. We’ll touch more upon customizability later in the article.
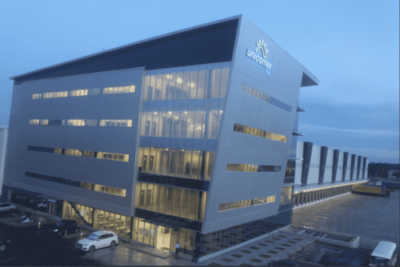
Preengineered steel building office tower with horizontal glass windows
One perceived a downside of long-spanning steel floors is that they tend to develop a “bouncy” characteristic over time. But thanks to superior damping, concrete tilt-up is much less likely to be plagued by this issue. However, builders can limit the deflection in steel floors by installing beams that possess higher rotational inertia.
Moreover, as steel members don’t require an overly complex foundation system, they’re a better option for construction sites with poor site stability. With concrete, cantilevering is much more expensive, as it demands carpentry and form set-up to hold the concrete in place until it cures. When you use steel joists for a cantilever, you only specify a full-depth cantilever or an extended end straight from the factory.
Also, you can use more glass on the project’s exterior with steel-framed structures. This greatly improves the building’s overall energy efficiency. Furthermore, it’s much easier and less-expensive to insulate a metal building compared to a concrete tilt-up one.
Overall, it’s safe to say that steel construction has the upper hand over tilt-up concrete in terms of customizability and versatility.

Commercial preengineered steel building architect office with garage doors.
Material Availability & Usage
As pre-engineered steel structures are generally transported from a factory to the construction site, this has an impact on the overall costs of the project. On the other hand, concrete tilt-up construction is generally performed on-site and materials such as wood and concrete can be locally sourced, thereby potentially reducing transportation costs.
However, steel arrives on site ready to be used whereas concrete has to be prepared on-site, a process which can face potential delays because of adverse weather conditions.
Time & Cost Savings
Pre-fabricated steel building kits are procured in an almost-complete form and can be assembled as soon as they arrive on the construction site. Furthermore, a metal structure can be erected regardless of whether the temperature is hot or cold. Concrete, on the other hand, requires warmer temperatures as it needs to be hoarded and heated. Tilt-up concrete also involves precise and accurate mixing of a wide variety of materials. This is a process which can consume a significant amount of time.
On average, the assembly and erection of a steel structure take about 33% less time compared to other construction methods. The installation costs of steel wall panel systems are generally on par with EIFs and synthetic stuccos, and considerably less than the ones in tilt-up concrete. This is because steel wall panel systems can be installed much faster than other systems, thereby resulting in significant time and labor-cost savings.
Although the cost of floors and frames is just a minor component of the overall cost of a project, selecting a steel frame results in a significantly reduced timescale compared to reinforced concrete construction. It also has a positive impact on a variety of other variable costs. These include cladding, labor, and foundation costs. This translates to significantly higher overall cost savings.
Furthermore, builders who opt for tilt-up concrete construction run the risk of facing delays caused by the shortage or lack of availability of key concrete-making materials such as cement. A variety of factors such as import policies and shipping rates can affect the availability and prices of cement.
Conclusively, metal buildings have significantly lesser fixed and variable costs compared to reinforced concrete construction.
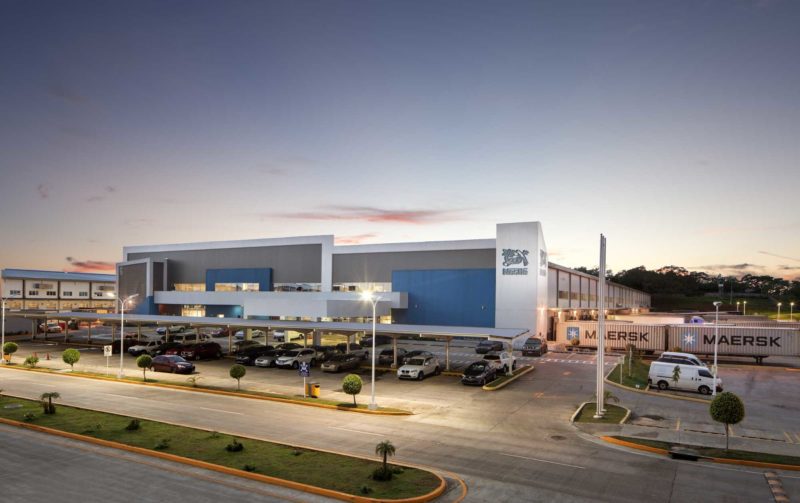
Commercial preengineered steel building in Panama
Recyclability
As it’s 100% recyclable, steel is a much more eco-friendly material than concrete. Lots of recyclable metal is sourced from demolishing old steel structures. This reduces the burden on the raw material mining industry and results in a manufacturing process that has a smaller environmental footprint. In the US, the long-span metal beams used in new steel buildings are made from around 95% recycled material. Thanks to the recyclability of steel, contractors can also benefit from LEED points. The owners of a metal building also get the opportunity to obtain a LEED certification. They can do this by utilizing energy-saving strategies that impact the complete cycle of a project, starting from eco-friendly construction practices right until the end of the project’s useful life. Effective strategies include opting for “greener” construction methods, materials and an array of other criteria. All of these will earn the project owner points towards their LEED certification.
Design Possibilities
Although concrete construction doesn’t offer as much customizability as metal construction, it does offer some real advantages in terms of space and its unique aesthetic. The main space-related benefit with high-rise reinforced concrete structures is that they require a less floor-to-floor height than metal structures. In other words, if both a steel structure and a concrete structure are 1,000 ft in height, the concrete one will typically have a greater number of floors. This provides more rentable space for building owners who opt for tilt-up concrete construction.
Furthermore, with proper engineering, the interruptions in a floor plate of a concrete building can be minimized as well.
Although steel structures require a higher floor-to-floor height than concrete buildings, engineers can use techniques such as castellated beam construction, a girder slab, and staggered truss to reduce the floor-to-floor height of the structure. However, when it comes to large floor spaces uninterrupted by columns, metal buildings reign supreme. Because of steels flexibility, builders can address the design requirements in different ways.
Durability against Natural Disasters
Compared to concrete, metal is a much more flexible and durable construction material. This means steel structures are much more resistant to natural disasters such as hurricanes, earthquakes, tsunamis. Thanks to the greater tensile strength and flexibility of the material, metal buildings can easily withstand levels of pressure which can easily wipe out traditional concrete structures.
There’s a reason why the Japanese use reinforced steel pipes in the construction of their buildings. Unlike concrete, which is brittle, steel is highly ductile and can absorb high levels of energy, which makes it the perfect material for construction in seismic zones. Thousands of people lose their lives due to concrete structures collapsing. Concrete tilt-up structures typically possess lightweight roofs which can become compromised under hurricane-force winds, thereby impacting the connections that hold the concrete panels together. A Home Depot store in Joplin, Missouri made global news when it was impacted by tornado winds exceeding 200 mph in speed. The tornado took the structure’s roof off and the large concrete walls, weighing in excess of 100,000 pounds, collapsed like dominoes. 7 individuals lost their lives.
However, when it comes to fire resistance, concrete holds an advantage over metal. As it can withstand fire for longer periods, a concrete building is less likely to come down in case a fire breaks out. Unlike steel, it doesn’t warp or melt when exposed to high temperatures over an extended period of time. However, constructors can improve the safety of metal buildings by spraying fire-proofing solutions on to the steel.
The Purpose of the Project
Tilt-up concrete buildings are best suited for projects that are likely to see heavy public traffic for years and years. Metal structures, on the other hand, are the best option for projects that won’t see such heavy use. Furthermore, if a steel structure is damaged due to a vehicle striking or another type of accident, the repairs will be much more expensive compared to a reinforced concrete structure. Consequently, the insurance costs of metal buildings are comparatively higher as well. However, steel buildings depreciate slower in value than concrete ones.
Typically, storage buildings such as warehouses and airplane hangars that are built with metal have more long-term durability and reliability. Tilt-up concrete construction, on the other hand, is more suited for buildings in which security is the greatest priority.
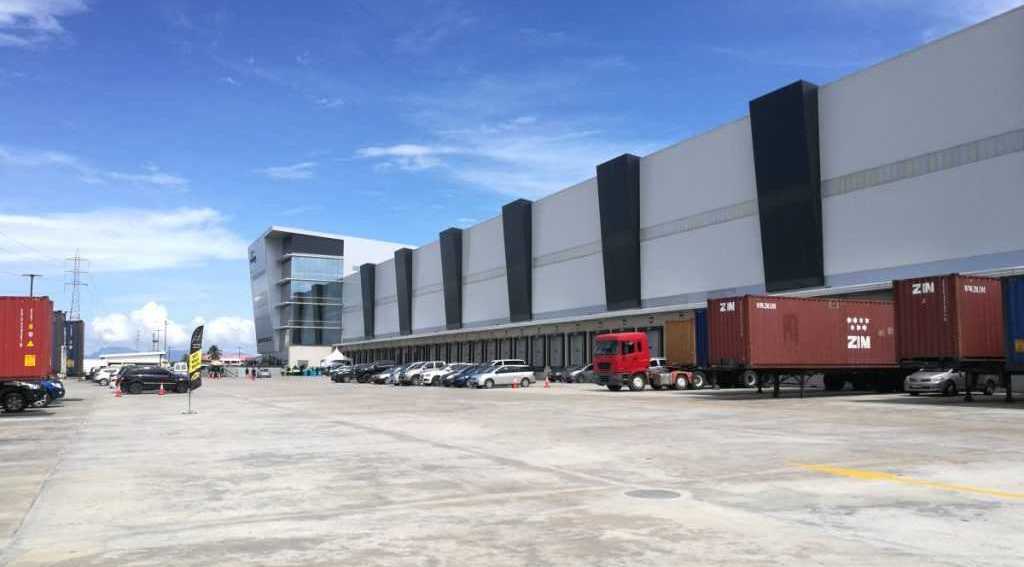
Commercial preengineered steel building in Trinidad
The Best of Both Worlds
Based on the project specifications and design requirements, buildings are often built with both steel and concrete to get the best qualities from both materials. Thanks to its versatility and customizability, modern pre-fabricated steel is more than capable of complementing tilt-up concrete structures. In fact, many new buildings are being built with a combination of prefabricated metal and tilt-up concrete.
About Allied Steel Buildings
At Allied Steel Buildings, no project is too big or small. Whether you are building a warehouse, garage, barn, or skyscraper, we excel in creating pre-engineered steel building solutions for clients large and small. Discover the Allied Steel Buildings difference and enjoy the peace of mind that comes with a premier building company. Call us today at 1.877.997.8335 to learn more or fill out the quote form below to price your building.
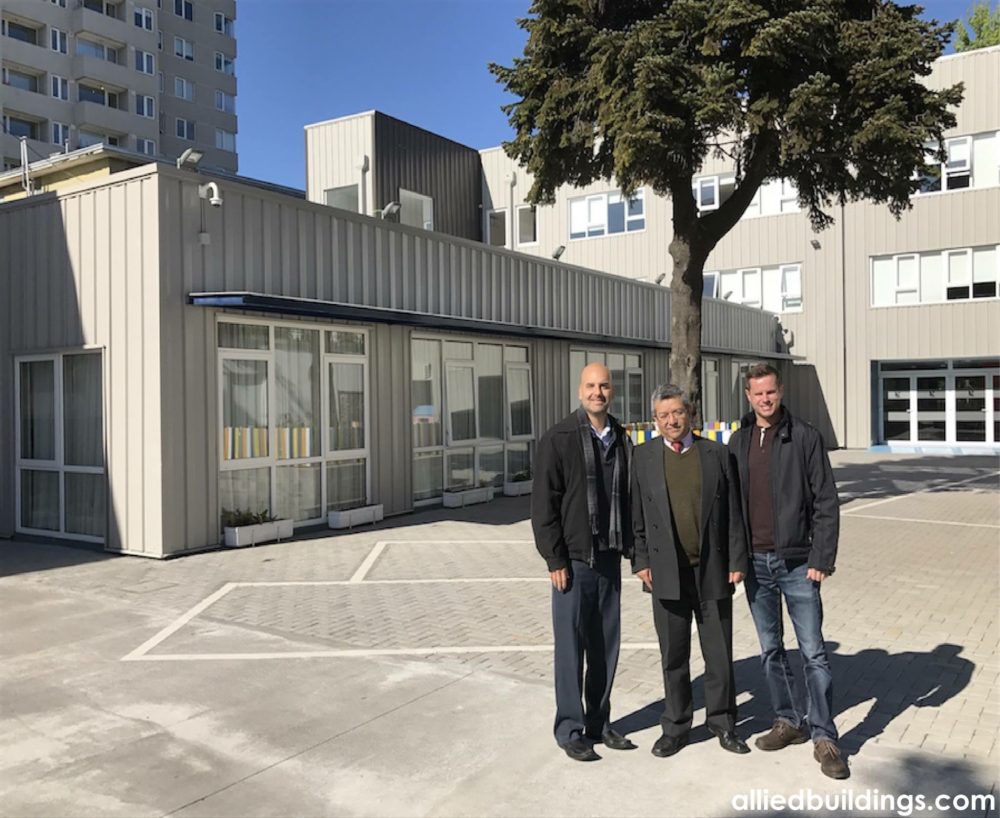
Preengineered multistory steel building school in Chile